UC San Diego Medical Center Improved Clean Room Scanning Rate By 46% With GLSS
Home Âŧ Case Study Âŧ UC San Diego Medical Center Improved Clean Room Scanning Rate By 46% With GLSS
California
Education
Patient Care
46%
UCSD Medical Center has a little angel in process improvement! Find out how Lily Angelocci helped save $4 million dollars for UCSD, which will help this nonprofit fund more programs for students and make a difference in healthcare.
THE CHALLENGE
In 2016 the New York Times reported a study that concluded $3 billion in cancer drugs are wasted annually in the US because they are distributed in vials that hold too much for most patients. Patients receive the proper dose and the remainder is discarded for safety reasons.
Due to this waste, cancer patients could face increased costs and drug availability issues. At the very least it exposes healthcare providers to heavy financial burdens to provide these treatments. To ease this burden the Centers of Medicare & Medicaid Services (CMS) will, with the proper documentation, reimburse the care provider for some of this waste. The problem? While UC San Diego Medical Center had installed new technology to compile the needed information, it did not have processes in place to capture the needed data when dispensing the drugs.
Lily Angelocci focused her project on an Oncology IV medication process. Lily and the team discovered that not every drug qualified for reimbursement. Based on this, they identified the top 23 most costly oncology drugs. These particular drugs were good to focus on since once prepared they had to be stored in a controlled environment and discarded after 6 hours if not used.
Lily completed a 12-month analysis of recent operations and determined the saving potential to be at least $4M. Because UC San Diego Medical Center is a nonprofit organization this revenue is slated to be invested in new programs to improve patient care and the care environment.
THE DISCOVERY
Realizing they could not focus on all 23 medications, Lily dove into the data thinking if they could focus exclusively on the top waste, that would save time and effort. Fortunately, the Pareto Principle applied and she found that 8 of the 23 oncology drugs amounted to 80% of the waste.
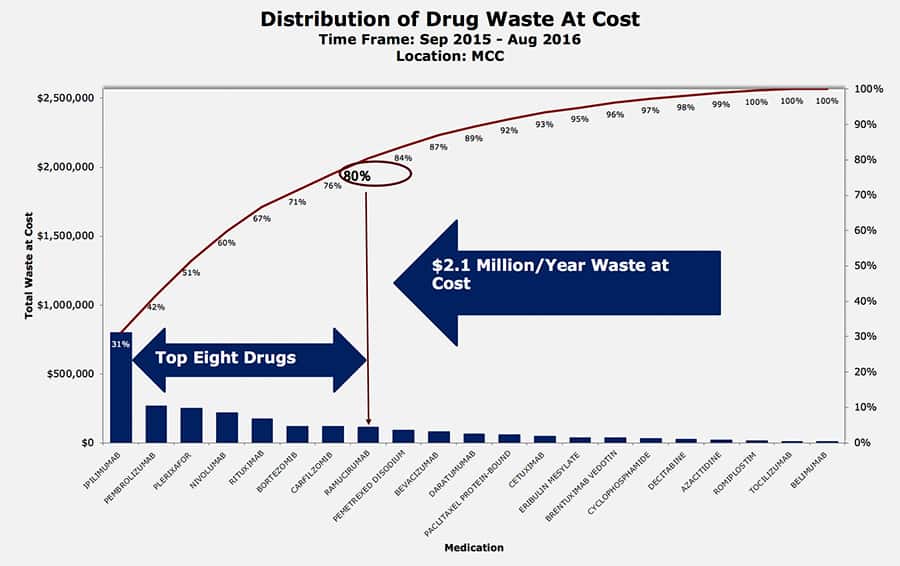
Next, it was time to look at the current process. The process was largely manual and staff were busy moving quickly to address patient needs. Lily was quick to note the staff seemed frustrated. They knew expensive drugs were being wasted but couldnât do anything about it. There was no process in place and it was not the fault of the staff.
In order to better understand what was happening in the process. Lily surveyed the staff. Key discoveries were:
- Staff was exhausted from running from the dispensing area to the IV Room
- Not all the equipment was in the right place
- Scanners did not work and significantly slowed down the process
- Not everybody was complying with the information recording
- There was no consistency on what information was captured
- Some drug information scanned easily and some did not scan at all
- Once scanned, some information did not import into the system
THE IMPROVEMENTS
Using a Fishbone Diagram developed from the survey information, Lily conducted a Rapid Improvement (Kaizen) Event with staff. They applied the 5 Whys and also identified many of the 8 Wastes in the process.
The improvements included:
- Mounting scanners at key location to avoid non-valued added motion
- Using touch screens for the system to avoid âgoing to sleepâ during non-valued added motion
- Standardizing processes, clarifying tasks and responsibilities
- Locating frequently used drugs to minimize travel
- Adding pharmacy staff on weekends to avoid bottlenecks
The Results
The 46% increase in scanning resulted in $3.73 million in annual revenue recovery. As mentioned, UC San Diego Medical Center is a nonprofit organization and plans to use the additional revenue to improve operations and patient care. For example, from this project three additional staff were added to support patient care. The remaining revenue recovery is slated to be used elsewhere in the medical center to further support the mission.
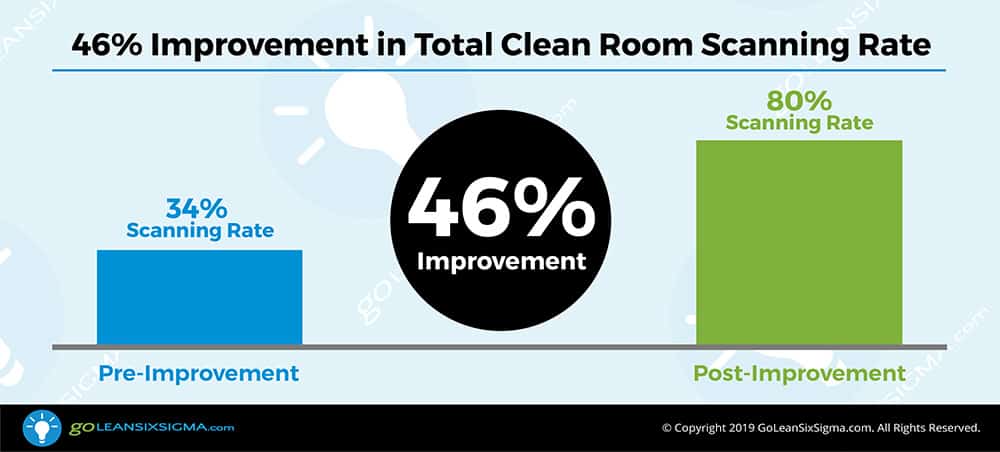
Whatâs Next
As is common, during the course of the project the team identified opportunities to reduce inventory levels and inventory discrepancy along with several opportunities to further improve the scanning process.
A key learning for the team was the need to stay focused on the process and avoid blaming anyone. As Lily stated, âItâs a structure issue and not a people issue.â It is safe to say that UC San Diego Medical Center has a âLittle Angelâ supporting their improvement journey.
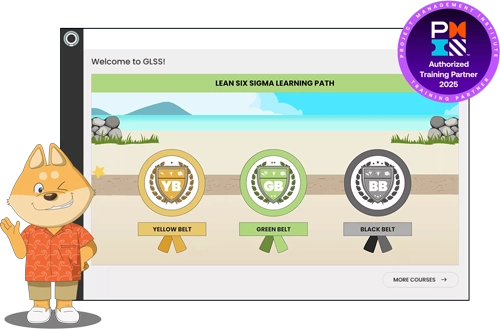
Start a free trial and get access to all GLSS courses (Yellow Belt, Green Belt, Black Belt, and more!) for only $499/year with GLSS Membership!